Optimización de los parámetros de rociado térmico del proceso de plasma para aplicación de recubrimientos de níquel
Por: Joel Moreno Palmerin1, Andrea Jezabel López González1, Eduardo Ugalde Mejía2, Oscar Rivera Domínguez3, Danielle Mazallupo3
Resumen
Se determinó el efecto de los parámetros de rociado térmico por plasma, a partir de considerar las variables como distancia de aplicación, velocidad del robot y número de ciclos. Los efectos de estas variables se midieron sobre las muestras recubiertas estimando el porcentaje de porosidad, porcentaje de partículas sin fundir, oxidos y espesor de recubrimiento. A partir de los resultados, se obtuvieron las mejores condiciones de deposito, es decir, se optimizó el proceso. Para esto se estableció un diseño de experimentos que permitió realizar un número representativo de pruebas, considerando cada una de las variables, así como los resultados de respuesta para su correlación, análisis y determinación de conclusiones. El propósito principal de la elección del número de ciclos de depósito y parámetros ajustados, es el de evidenciar el desarrollo y comportamiento de las variables de respuesta a lo largo y ancho del proceso sobre los recubrimientos, así como generar la repetitividad experimental que asegure el mejor comportamiento de las variables durante el proceso de deposición.
Abstract
The effect of plasma thermal spray parameters was determined by considering variables such as application distance, robot speed, and the number of cycles. The effects of these variables on the coated samples were measured by estimating the porosity percentage, percentage of unmelted particles, oxides, and coating thickness. Based on the results, the optimal deposition conditions were identified, thereby optimizing the process. To achieve this, an experimental design was established, allowing for a representative number of trials while considering each variable and its corresponding response results for correlation, analysis, and conclusion determination. The primary purpose of selecting the number of deposition cycles and adjusted parameters was to demonstrate the evolution and behavior of the response variables throughout the coating process, as well as to ensure experimental repeatability that guarantees the best performance of the variables during deposition.
Introducción
La súper aleación de niquel 718 es una de las más utilizadas hoy en día en aplicaciones aeroespaciales.[1] El rociado por plasma atmosférico (APS (Atmospheric Plasma Spraying) es la técnica de rociado térmico utilizada en el desarrollo de este trabajo, para realizar los depósitos de la aleación de inconel 718 como material de relleno en componentes aeronáuticos. Tal acción tiene como finalidad la restauración dimensional de las partes debido al desgaste que sufren al estar sujetos a determinadas condiciones de operación. La técnica involucra tres diferentes pasos; formación del plasma spray, inyección de polvo y formación de recubrimiento.
Fundamento teórico
Rociado térmico
El rociado térmico se describe como la familia de procesos que hacen uso de energía térmica, generada de manera química o eléctrica para fundir o ablandar y acelerar partículas.[1] El comportamiento del material que interactúa bajo estas condiciones de funcionamiento, le permite generar las altas temperaturas y la velocidad de partícula que inducen a cierta deformación en la gota al momento de impactar en la superficie, adhiriéndose a la superficie del substrato a través de una dispersión de corriente continua de partículas fundidas para formar delgadas capas continúas solidificadas.[1]
Rociado por Plasma Atmosférico
El proceso de rociado por plasma atmosférico o aire por sus siglas en inglés APS (Atmospheric Plasma Spraying) es uno de lo más utilizados por la industria aeronáutica, la industria de la generación de energía y la industria automotriz, el cual tiene como principal característica generar la temperatura del estado plasma mediante un gas inerte que es generalmente argón o una mezcla de argón con helio, nitrógeno o hidrógeno; es calentado a través de un arco de corriente directa (fig. 1). El proceso también involucra manejar potencias en un rango de 20 a 200 kW. [1]
Ventajas del proceso de rociado térmico
Una de las principales ventajas de dicho proceso es el bajo consumo de materia prima y el desempeño de depósito alcanzado.[1] Gracias a estas características los recubrimientos mejoran las condiciones de degaste y corrosión debido a la modificación en propiedades mecánicas, físicas y químicas, además de mejorar la apariencia superficial de mejor calidad.
Aplicación del rociado térmico en la industria aeronáutica
Una de las grandes aplicaciones de estos recubrimientos es en revestimientos cerámicos para barrera térmica, conocido como TBC (Thermal Barrier Coating). Son utilizados como protección de componentes metálicos que sufren degradación debido a corrosión, oxidación o sobrecarga de calor excesivo durante el servicio en ambientes térmicamente drásticos.
En la industria aeronáutica, uno de los materiales utilizados como materia prima es la aleación inconel 718, la cual se aplica como recubrimiento o material de reparación, debido a que posee un punto de fusión elevado, excelente resistencia mecánica, a la corrosión, a la fluencia, a la fatiga y a la fractura, es por ello que este material resulta ser demasiado atractivo, para utilizarla en el proceso APS,[6]. Sin embargo, el proceso modifica las variables en función del material a utilizar, es por ello que el presente trabajo tiene como objetivo estudiar los parámetros del APS como, distancia de la pistola de plasma, velocidad del robot, ciclos de trabajo y su efecto sobre las variabes de respuesta como son: porosidad, partículas sin fundir y microdureza del recubrimiento, esto permitirá optimizar las variables del proceso.
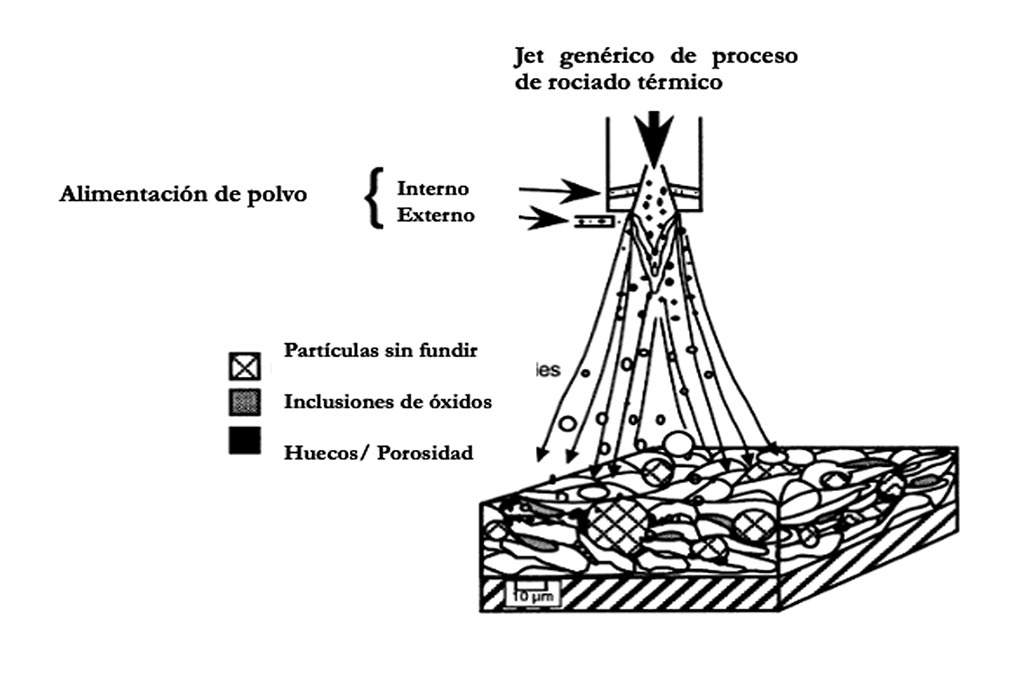
Desarrollo experimental
El diseño del tema yace de la retrospectiva del proceso hacia la mejora en las características del producto (recubrimiento) mediante el estudio del efecto de los parámetros de procesamiento en razón a su experimentación, descripción fenomenológica y análisis de resultados que lograron ser comparables.
- Para el desarrollo del trabajo, se planteó la siguiente secuencia de experimentos;
- Identificar los parámetros de procesamiento operacionales, tipo de respuesta, así como los valores de importancia.
- Seleccionar la matriz de diseño de experimentos necesaria.
- Conducir los experimentos apegado a la matriz de diseño.
- Preparación de muestras y recopilación de respuestas (Medición de porosidad, óxidos, espesor y partículas sin fundir).
- Conducción de optimización gráfica y numérica.
Conclusiones y resultados
Para el tratamiento de los datos obtenidos se utilizaron procedimientos estadísticos descriptivos e inferenciales en el revelado de propiedades, tendencias y relaciones de las características para la valoración e interpretación de resultados. La tabla 1. presenta el diseño de experimentos tomando en consideración las variables del proceso para obtener las variables de respuesta.
Secuencia de pruebas realizadas
Se realizaron 5 series de pruebas, divididas en dos grupos, con cuatro pruebas cada una. En cada serie hubo una secuencia de repetición de ciclos. Se consideraron dos velocidades de aplicación, para el grupo 1 se consideró la velocidad de 1 mm/s, mientras que para el grupo dos se utilizó una velocidad de 5 mm/s.
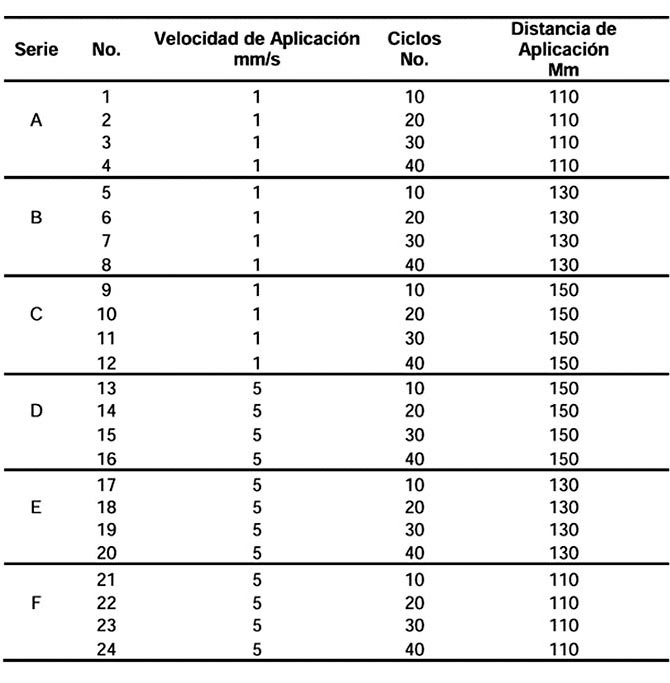
Caracterización de la materia prima
Se procedió a la caracterización de la materia prima (polvo y sustrato) utilizando las técnicas de preparación metalográfica, microscopia óptica, microscopia electrónica, difracción de rayos X y fluorescencia de rayos X, esto permitió determinar microestructura, morfología, composición química, así como fases presentes. La figura 2a corresponde a la sección transversal, la cual muestra la microestructura característica de la aleación de inconel 718, no se obsevaron fases presentes. Así mismo, la figura 2b presenta la morfología del polvo con apariencia en su mayoría esférica. (ver fig. 2).
Depósito del recubrimiento
El depósito del material sobre las muestras se llevó a cabo en la estación de depósito de rociado térmico con proceso plasma. Esto se resume en una cámara aislada que contiene una mesa redonda con varios grados de libertad y un brazo robótico. La mesa fue colocada a un ángulo de ciento ochenta grados, paralela al piso, gira en sentido contrario de las manecillas del reloj a determinadas revoluciones. Sobre la mesa se coloca un soporte cilíndrico con las dimensiones del diámetro de la mesa, en la cual se sujetan las muestras entre la superficie con orificios del soporte y un tornillo que fija y mantiene paralela la superficie de la muestra a la de la mesa.
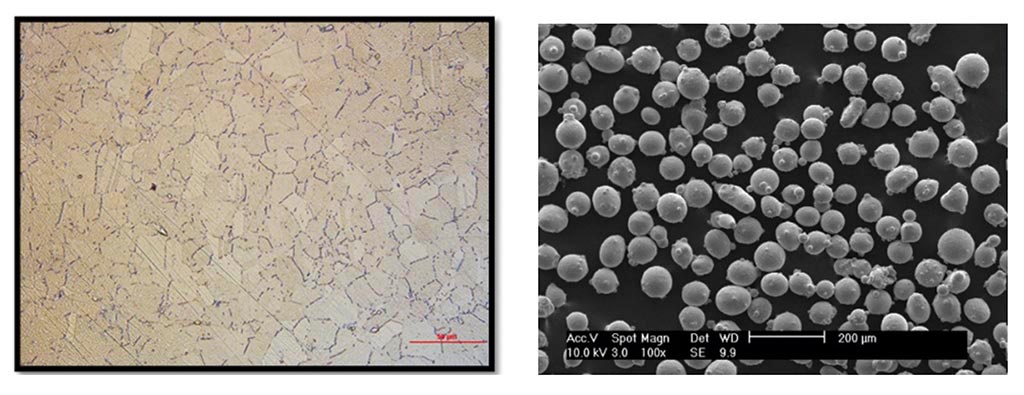
La posición de la pistola una vez iniciado el proceso y a lo largo de él, se mantiene a noventa grados de la superficie de la muestra. La pistola tiene un tiempo de estabilización de temperatura de plasma y flujo de polvo de un minuto para homogenizar las condiciones de depósito una vez que comienza el proceso.

Análisis de fracción superficial
Aquí se describe el proceso de caracterización de las variables de respuesta que representan mayor importancia sobre los recubrimientos, para ello se divide en diferentes secciones. Los puntos muestrales se tomaron después de 5 mm a partir de los bordes de cada muestra y en 150 μm. Se tomaron cinco segmentos de muestra a 200 aumentos a lo largo de la sección transversal del recubrimiento para cada una de las muestras, como se ilustra en la imagen (fig. 3).
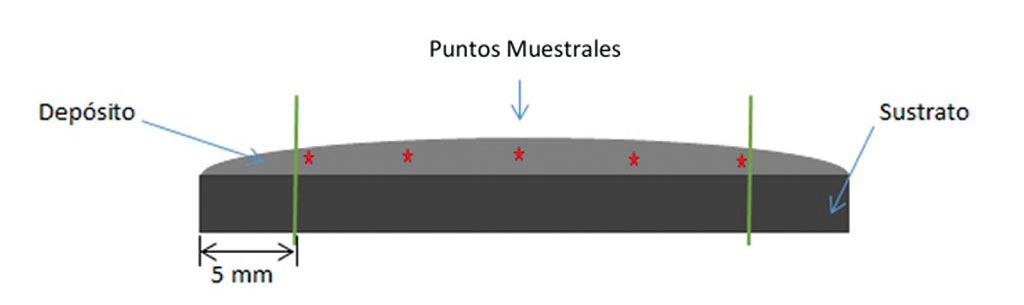
determinar las variables de respuesta.
Resultados
Como resultados, se presenta la composición química vía fluorescencia de rayos X de la materia prima (polvo y el sustrato), así como el efecto de las variables del proceso sobre las variables de respuesta como son; porosidad, partículas sin fundir, óxidos y espesor de recubrimiento.
Composición química
Se obtuvo la composición química del sustrato y del polvo por medio de fluorescencia de rayos X, y como se puede observar, la composición entre ambos materiales es muy similar, lo cual corresponde con la literatura para una aleación de inconel 718, es decir, ambos materiales corresponden.
Los resultados de los valores para cada elemento se pueden observar en la tabla 2.
Preparación metalográfica
Se realizó la preparación metalográfica sobre la sección transversal y longitudinal para cada muestra, basados en la norma ASTM E3 – 01, ambas muestras fueron cortadas de una placa metálica con disco de diamante. Posteriormente, las muestras fueron montadas en caliente utilizando baquelita, el desbaste se realizó con lijas de SiC y el pulido se llevó a cabo con alúmina.
La figura 4 muestra la sección transversal donde se puede observar cada una de las condiciones del material base y del recubrimiento.
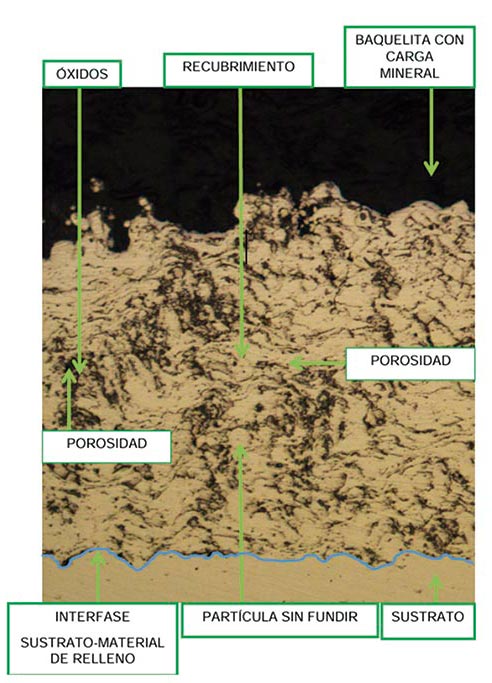
Comportamiento de la porosidad
El compartamiento de la porosidad en función de las variables del proceso se ve afectada de manera considerable por la combinación de la velocidad y el número de ciclos, la porosidad incrementa de manera lineal con la distancia de aplicación y de igual manera con la velocidad, sin embargo, dentro de las variables a considerar, la velocidad no tiene efecto significativo sobre esta variable. El diagrama de pareto de la figura 1, ilustra dicho comportamiento de manera mas simplificada en función de los resultados obtenidos a través del diseño de experimentos.
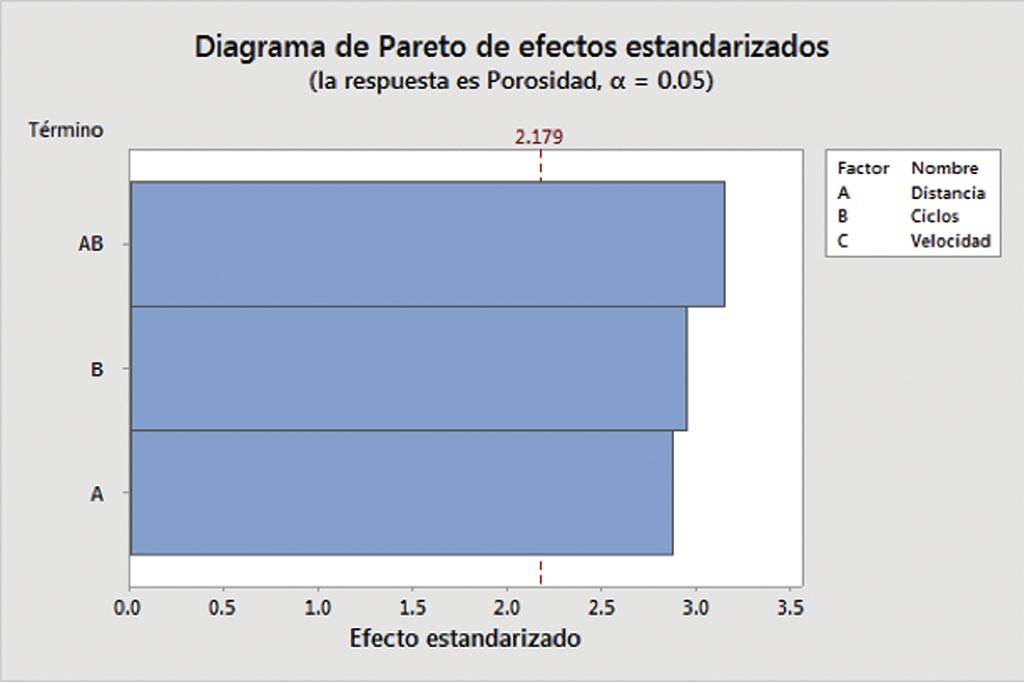
ciclos sobre la variable de porosidad.
Comportamiento de los óxidos
El número de óxidos presentes en el recubrimiento, tuvo un incremento respecto a la distancia y la velocidad de aplicación, los valores se mantienen dentro de un rango (23-26%) de acuerdo con los parámetros seleccionados. Sin embargo, el porcentaje de óxidos incrementa de manera considerable con las variables antes mencionadas de manera independiente. Por lo tanto, la combinación de los factores velocidad y distancia de aplicación no presentaron mayor efecto para el incremento de la presencia de óxidos. La figura 2, ilustra el comportamiento de las variables del proceso respecto a la respuesta del número de óxidos.
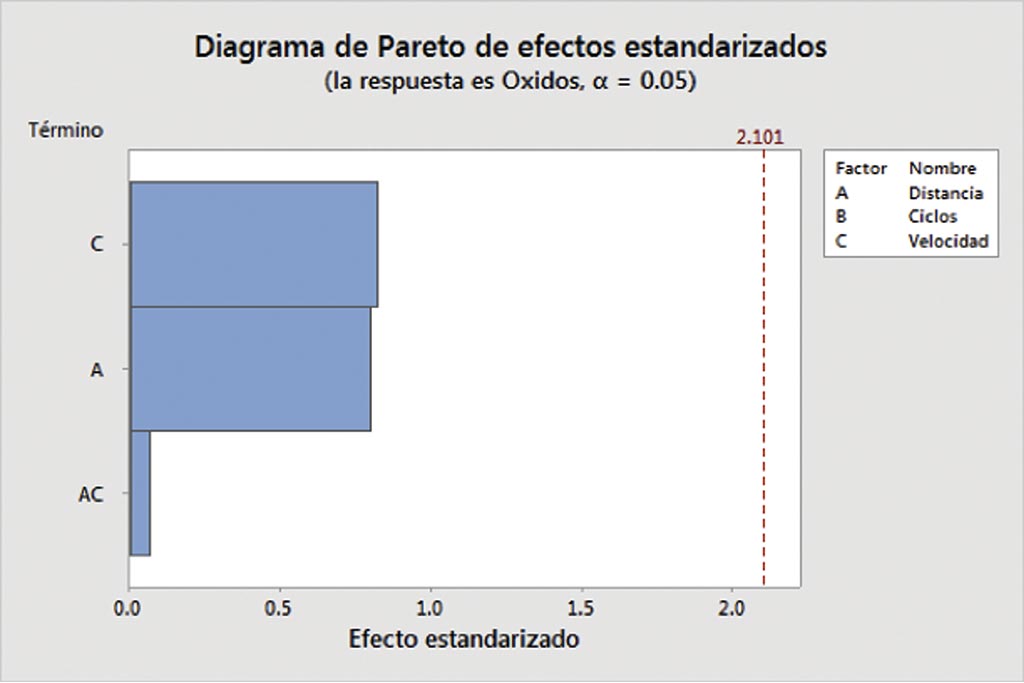
velocidad sobre la variable del porcentaje de óxidos presentes en el recubrimiento.
Comportamiento de las Partículas sin fundir
El comportamiento de las partículas sin fundir se ve afectado, incrementando conforme aumenta el número de ciclos. Sin embargo, con el incremento de la velocidad del robot hay un efecto que no es significativo, para el caso de la distancia de aplicación o de trabajo no se considera relevante, por lo tanto, en el diagrama de pareto no se hace evidente, debido a su poca influencia. En resumen, el número promedio de partículas sin fundir presenta un incremento en función del aumento del número de ciclos. La combinación de las variables de los ciclos y la velocidad de aplicación no son significativas en comparación cuando se analizan de manera independiente. La figura 3, ilustra el comportamiento en el diagrama de pareto para el porcentaje de partículas sin fundir.
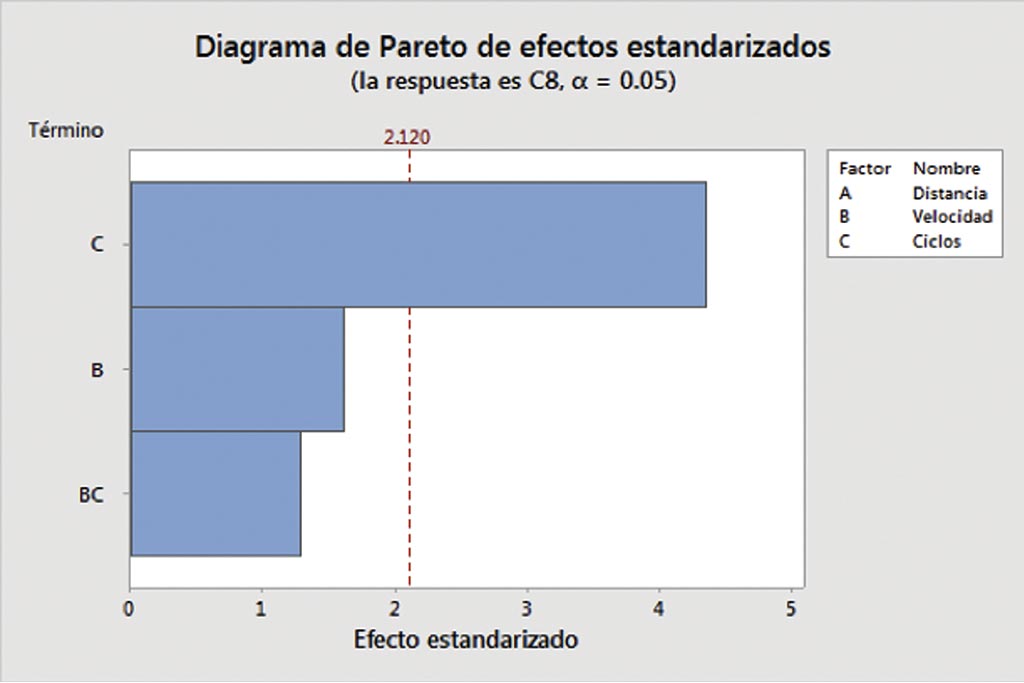
el número de ciclos sobre el porcentaje de partículas sin fundir.
Comportamiento del Espesor/Ciclos
El espesor resulta en un comportamiento creciente en función del número de ciclos y con la velocidad de aplicación, analizando los parámetros de manera individual. Sin embargo, dicho espesor tiende a disminuir con la distancia de aplicación. Por otra parte, aún y cuando la combinación de ambas variables tienen efecto siginificativo sobre el espesor del recubrimiento, no se compara con el efecto individualizado de cada variable. En el diagrama de pareto de la figura 4, se observa el efecto de los factores combinados e individuales sobre la relación espesor/ciclos, observando que a mayor número de ciclos mayor efecto sobre el espesor.
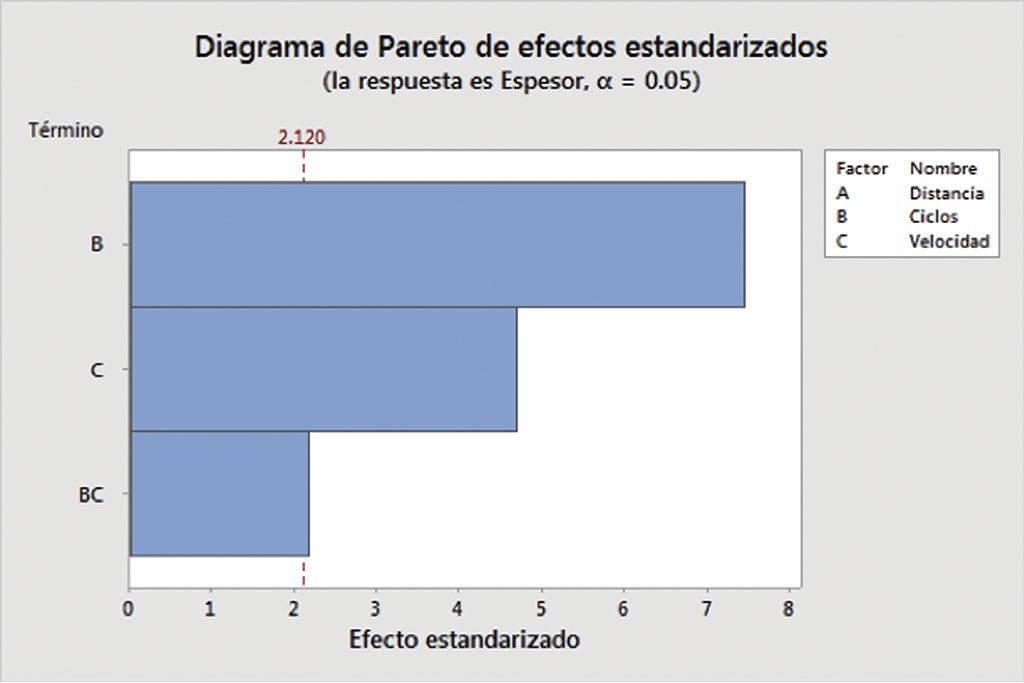
y velocidad de aplicación sobre el espesor del recubrimiento.
Conclusiones
El efecto de las variables cinemáticas de procesamiento (distancia de aplicación, velocidad de aplicación y el número de ciclos) sobre las variables de respuesta (porcentaje de porosidad, porcentaje de óxidos, número de partículas sin fundir y espesor) han sido investigadas en recubrimientos de aleación 718 aplicados por rociado con plasma atmosférico.
- VII. De manera individual, la velocidad de aplicación y el número de ciclos son las variables de aplicación que de manera individual tienen mayor efecto sobre las variables de respuesta.
- VIII. La velocidad de aplicación es una de las variables de aplicación que menos efecto tiene sobre cada una de las variables de respuesta, sin embargo, su efecto es significativo para el espesor de recubrimiento al igual que el número de ciclos, ambas de manera individual; asímismo, cuando ambas se analizan de manera combinada presentan un comportamiento importante sobre el espesor del recubrimiento.
- IX. La distancia de aplicación en combinación con el número de ciclos tiene un efecto exponencial sobre el incremento del porcentaje de porosidad.
- X. El número de ciclos afecta de manera significativa al número de partículas sin fundir.
- XI. Los resultados experimentales se ajustan apropiadamente con el estudio estadístico realizado mediante el diseño de experimentos. Lo cual permitió observar que las condiciones mas apropiadas de procesamiento respecto a las variables de respuesta corresponden a una distancia de aplicación de 150 mm, velocidad de aplicación de 5 mm/s y 40 ciclos depositados.
Agradecimientos
Los autores agrdecen el apoyo brindado a la empresa SAFRAN Group, por todas las facilidades, materias primas y apoyo brindado para la realización de este trabajo. Así como, la dedicación y compromiso del Ing. Oscar Rivera Domínguez, sin él este trabajo y colaboración no hubiera sido posible. Así mismo, queremos agradecer al Laboratorio Nacional de Investigación y Desarrollo Tecnológico de Recubirmientos Avanzados LIDTRA, por todas las facilididades otorgadas para el análisis y caracterización de las pruebas a través de la Maestra Cristina Daniela Moncada Sánchez.
Referencias bibliográficas
- [1] J.R. Davis (2004), Handbook Thermal Spray Technology. https://books.google.com.mx/books?hl=es&lr=&id=S0PryYc9T70C&oi=fnd&pg=PA3&%20110%20dq=davis+j.r.+2003.+handbook+of+thermal+spray+technology&ots=m7%20SWRZpHs&sig=dKGNuvwrRpT82N11CxVfUBlvYvo#v=onepage&q&f=true
- [2] Carlos Alberto Guevara Chávez (2011) RECUPERACIÓN DE DADOS PARA ESTAMPADO DE ACERO GRADO D2 MEDIANTE PROCESOS DE SOLDADURA NO CONVENCIONALES. https://comimsa.repositorioinstitucional.mx/jspui/bitstream/1022/56/1/Tesis%20de%20Maestria%20Carlos%20Guevara%20SIN.pdf
- [3] Morán García. D., Ramírez Pérez D. (2008) CARACTERIZACIÓN DEL PROCESO DE ROCIADO TÉRMICO DE ACERO INOXIDABLE SOBRE ACEROS DE BAJO CONTENIDO DE CARBONO. http://www.ptolomeo.unam.mx:8080/xmlui/handle/132.248.52.100/1208
- [4] Marulanda Arévalo, J. L., Tristancho Reyes, J. L., & Gonzáles B, H. Á. (2024). LA TECNOLOGÍA DE RECUPERACIÓN Y PROTECCIÓN CONTRA EL DESGASTE ESTÁ EN EL ROCIADO TÉRMICO. http://www.scielo.org.co/scielo.php?script=sci_arttext&pid=S169282612014000100009#:~:text=Los%20recubrimientos%20por%20rociado%20t%C3%A9rmico,de%20funcionamiento%20a%20la%20superficie.
- [5] José Luddey Marulanda Arévalo, José Luis Tristancho Reyes, Héctor Álvaro Gonzáles B. (2014). LA TECNOLOGÍA DE RECUPERACIÓN Y PROTECCIÓN CONTRA EL DESGASTE ESTÁ EN EL ROCIADO TÉRMICO. https://dialnet.unirioja.es/descarga/articulo/4847260.pdf
- [6] C F Elefterie (2017) Aeronautical requirements for Inconel 718 alloy. IOP Conf. Series: Materials Science and Engineering. 209 012060. 1-6. Doi: 10.1088/1757 899X/209/1/012060.
1. Universidad de Guanajuato, Departamento de ingeniería en Minas, Metalurgia y Geología,
2. Instituto Tecnológico de Querétaro. Av Tecnológico S/N, Centro Histórico, Centro, 76000 Santiago de Querétaro, Qro.
3. SAFRAN – Group, Parque Industrial Aeroespacial de Querétaro, 76278 Galeras, Qro.